인터넷이 보편화된 지 20여년 밖에 지나지 않았지만 소비자들의 삶을 크게 바꾸었으며, 구글, 페이스북, 아마존과 같은 거대기업들도 탄생했다.
이제 인터넷이 IoT 기술을 기반으로 산업인터넷이란 형태로 산업계에 확장되어 가고 있다.
이러한 산업인터넷은 반도체기술, 통신기술, 센서기술, 인공지능의 기술과 맞물리며, 또 한 차례 산업의 큰 격변을 몰고 올 것으로 전망된다.
이러한 변화에 발빠르게 대응하기 위한 움직임도 가시화되는 중이다.
독일의 인더스트리 4.0, 미국의 IIC(Industrial Internet Consortium) 등에서와 같이 국가적인 차원에서 혹은 산학연대, 기업간 컨소시엄 등의 형태로 새로운 제조업 혁신, 나아가 산업 생태계의 혁신을 향한 노력들이 시작되고 있다.
그러나 한편으로는 이러한 프로그램들에 회의적인 시각들도 적지 않다.
인더스트리 4.0이 마케팅 용어로 사용되 면서 그 의미가 점점 과장되어 가고 있으며 몇 년 안에 잊혀진 단어가 될 수 있다는 경고도 있다.
그만큼 이 상적인 비 전보다는 이 프로그램들을 통한 가시적인 성과를 요구하고 있기도 하다.
추진 주체들은 스마트 팩토리에서 그 답을 찾고 있다.
실제로 대부분의 프로그램이 스마트 팩토리 구축을 최우선 과제로 선정하고 있다.
당장은 스마트 팩토리에서 시작되고 있지만 단일 공장에서 여러 공장간의 연결, 공급망과의 연계 등으로 확 장되 며, 점차 서비스화로 진화될 것이다.
충족하려는 수요 역시 좋은 제품, 값싼 제품에서 맞춤형 제품으로, 궁극적으로는 수요의 목적, 제품구매의 이유(Why behind Buy)를 찾아 근본적으로 해결하려는 방향으로 갈 것 으로 전망되고 있다.
예를 들어 안전하고 빠르고 쾌적한 항공서비스를 저렴한 합리적인 가격에 제공하기 위해서는 항공 엔진의 성능, 항공기 정비, 항공기 노선 조정 등이 모두 유기적으로 연결되어야 경쟁력 있는 서비스가 가능해진다.
즉 단일 기업이 모든 문제를 해결할 수 없고 관련 생태계의 기업들과 유기적으로 연계되어야 한다.
미국의 IIC가 추구하는 것의 상당 부분도 궁극적으로 연결 협력할 수 있는 생태계의 조성에 맞춰져 있다.
산업인터넷 혁명은 개념적으로 보일 수 있다.
사례도 아직 일부 분야에 머무르고 있고 보편적인 트렌드가 될 수 있 을지 회의적인 시각들도 있을 수 있다.
그러나 시간이 좀 걸릴 수는 있을지 몰라도 그 방향은 크게 달라지지 않을 것이며 산업계의 판도를 바꾸고 경계를 지워갈 것이다.
스마트 팩토리는 단지 그 변화의 서곡에 불과할 가능성이 크다.
세계 각국 정치 및 경제 리더들이 모여 글로벌 현안에 대해 논의하는 다보스 포 럼(세계경제포럼, World Economic Forum)은 매년 세계인의 이목을 끌고 있다.
올 1월에 있었던 다보스 포럼의 화두는‘4차 산업혁명의 이해(Mastering the 4th Industrial Revolution)’였다.
전세계가 주목하는 자리인 만큼, 전문가는 물론 일반 인들까지 4차 산업혁명에 대한 관심을 갖는 계기가 되었다.
증기기관으로 대표되는 1차 산업혁명, 대량생산의 2차 산업혁명, IT(Information Technology, 정보기술)에 의한 3차 산업혁명에 이은 4차 산업혁명은 디지털 기기와 인간, 물리적 환경의 융합을 통해 이루어질 것이라고 한다.
산업현장에 있는 다양한 센서와 기기들이 스스로 정보를 취합하고, 취합된 정보를 바탕으로 생산성을 최대 로 끌어 올릴 수 있는, 인공지능이 결합된 생산시스템에 대한 기대를 불러 일으키고 있다.
선진국을 중심으로 이러한 움직임이 가시화 되고 기대가 커지고 있는 데에는 선진국 제조업의 위기감이 자리잡고 있기도 하다.
1. 선진국 위협하는 신흥 제조국의 성장
선진국들은 컨베이어 벨트 기반의 대량 생산, 부품 공용화, 모듈화 등 제조업의 혁 신에 힘입어 오랫동안 산업 발전을 이끌어 왔다.
하지만 낮은 인건비나 지대 등을 바탕으로 가격 경쟁력을 내세운 개발도상국의 추격은 선진국 제조업을 압박하고 있다.
생산 장비 등의 기술이 보편화되면서 이제는 신흥국 기업들도 선진 제조기업의 생산 기술을 상당 부분 따라잡을 수 있게 되었다.
제조경쟁력의 핵심이 되어 온 핵심부품, 소재, 특허, 설비 등의 독점적 활용이 어렵게 됨에 따라 고유의 차별적 가치 확보도 역시 어려워졌다.
선진 제조기업간의 경쟁이 격화되는 가운데 중국 등 신흥국의 추격이 두드러지면서 선진국의 제조업 위기감은 커져 왔다.
중국(북경)의 경우, 인건비가 독일(뒤셀도르프) 대비 1/7 수준, 우리나라(서울) 대비 1/3 수준에 불과하다(2014 제조업 종사자 평균 임금 기준).
중국의 최저임금은 약 10년 전부터 거의 매년 두 자릿수의 증가율을 보일 만큼 가파르게 상승해 왔음에 도 불구하고 여전히 선진국의 제조업체에 충분히 위협을 가할 수 있는 수준이다.
베트남 등 동남아 국가들은 중국에 비해서도 임금이 훨씬 낮은 수준이다.
신훙국의 기술적 진보도 빠르게 일어나고 있다. 중국은 선진국 기업들의 위탁 생산과 기술협업을 통해 상당한 기술적 진보를 이루어냈다.
샤오미 화웨이와 같은 기 업들은 선진 기업들을 위협하고 있다. 선진기업에 근접한 기술력에 가격경쟁력까지 더해져 압도적인 가성비로 시장에서 좋은 평가를 받고 있다.
기술력의 지표로 활용 되는 특허 출원 측면에서도 2011년을 기점으로 중국은 이미 일본, 미국, 한국의 출 원 건수를 넘어선 바 있다.
이처럼 가격경쟁력에 기술력까지 확보한 신흥국 기업들 은 선진국의 제조업에 상당한 위협이 되고 있다.
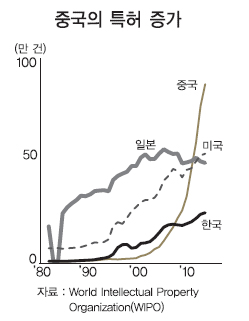
2. 제조업 부활 프로젝트 핵심, 스마트 팩토리
개도국의 추격을 따돌리고 혁신을 도모하기 위해 선진국들은 제조업 부활 프로젝트 를 추진 중이다. 각국별로 인더스트리 4.0, 산업인터넷, 스마트제조, 첨단제조 등 다양한 프로그램이 가동되고 있다.
독일의 인더스트리 4.0
제조업 강화 전략 가운데 가장 널리 알려진 것은 독일의 인더스트리(Industrie) 4.0 이다.
2011년 하노버 산업박람회에서 처음 용어가 사용된 데 이어 인더스트리 4.0 은 산학연 협력 프로그램으로 가동 중이다.
IoT(Internet of Things, 사물인터넷), 클라우드 컴퓨팅, 빅데이터 등 주요 ICT 기술을 제조업에 적용하여 이를 좀더 발전 된 형태로 만들어 보겠다는 것이 이 프로젝트의 목표이다.
ABB, BASF, BMW, 보 쉬(Bosch), 다임러(Daimler), 인피니언(Infineon Technologies), SAP, 지멘스 (Siemens), 티센크루프(ThyssenKrupp), 트럼프(TRUMPF) 등 독일의 대표 제조기업들이 이 프로그램에 참여하고 있다.
독일 정부 및 학계, 대표 업체들이 참여한 만 큼 전세계의 많은 관심을 받고 있어, 인더스트리 4.0은 4차 산업혁명과 같은 의미로 사용되기도 한다.
독일 정부는 인더스트리 4.0의 성공 사례를 만들기 위해 스마트 팩토리 구축에 집중하고 있다.
학계 주도로 선행 연구를 진행하며, 학계의 연구를 기반으로 산업계가 스마트 팩토리를 구축하고 실현하는 것이다.
지멘스의 암베르그(Amberg) 공장, 지멘스와 SAP의 장비 및 솔루션을 적용한 BMW 공장 등이 대표적인 도입 사례이 며, 중국 내 공장으로의 확산도 목표로 하고 있다.
미국의 첨단제조 프로그램
미국 정부도 제조업의 부활과 신흥국으로 이전한 공장들을 미국으로 회귀시키기 위한 리쇼어링 강화 정책의 일환으로 첨단 제조(Advanced Manufacturing), 스마트 제조(Smart Manufacturing)를 위한 R&D 예산 확충 및 프로그램 시행을 추진하고 있다.
연방정부 주도로 발족된 연구개발 컨소시엄인 SMLC(Smart Manufacturing Leadership Coalition)를 통해 지능형 시스템을 공장에 적용하려 는 시도도 하고 있다.
미국의 경우 정부 프로그램뿐 아니라 민간 프로그램이 발달했다는 특징이 있다.
대표적인 것이 IIC(Industrial Internet Consortium)로 GE, IBM, Intel, Cisco, AT&T, SAP 등에 의해 2014년 설립되었다.
현재 200여 개의 기업이 참여하며 제조업 강화 프로그램의 실질적인 중추 역할을 하고 있다.
산업 인터넷 기술의 발전과 적용 확산을 촉진하며 이를 위해 참조 모델(reference architecture), 보안체제 (security framework), 공개표준 등을 통한 산업 생태계 조성을 지향하고 있다.
민간 프로그램인 만큼 학술적인 색채보다는 실용성이 강해, 독일보다 뒤늦게 출발했 음에도 불구하고 주목할 만한 케이스들을 양산해내고 있다는 평가를 받는다.
일본의 IVI
일본의 경우도 장기 불황을 극복하기 위한 아베노믹스의 한 축으로 제조업 혁신을 추진 중이며, 산업재흥전략, 로봇신전략 등을 통해 첨단 설비 투자를 유도하고 로봇 산업의 육성을 희망하고 있다.
이러한 가운데 일본 기계학회를 중심으로 IVI(Industrial Value-chain Initiative)가 발족되었다. 이 프로그램은 공장마다 서로 다른 규격으로 운영되고 있는 설비 간에 데이터 전송이 가능하도록 통신규격과 보안기술의 표준화를 추진하고 있다.
이를 통해 공장 간의 연결을 강화하여, 부품의 생산에서 최종 제품의 조립까지를 자연스럽게 이을 수 있는 생태계를 구축하겠다는 것이다.
제조업 강화 프로그램에 대한 기대
이러한 프로그램에 대해 업계의 기대도 크다.
맥킨지 컨설팅이 업계 전문가를 대상 으로 한 설문 조사에 따르면 제조업 강화 프로그램의 경쟁력 향상 효과와 발전 잠재력에 대해 긍정적으로 답한 응답자는 90%에 이르는 것으로 나타났다.
특히 이러한 프로그램이 1년 전의 기대와 얼마나 달라졌냐는 질문에 대해 변하지 않았거나 더 긍 정적이라는 응답이 80~90% 가량인 것으로 나타나, 업계의 기대가 큰 것으로 파악 된다.
다만 아직까지 제조업 강화 프로그램으로 인한 효과를 체감했다는 응답은 40% 수준에 머무르면서 업계의 기대가 다소 감소할 여지는 있어 보인다.
실제로 이러한 프로그램들에 회의적인 시각들도 적지 않다.
미텔슈탄트(Mittelstand)라고 불리는 독일의 핵심 중견 기업들 도 인더스트리 4.0 프로그램을 어떻게 따라갈 것인지에 대해 고민이 많다
고 보도되고 있다. 중소기업들은 비용 및 관련 지식 부족, 표준화 미흡 등으로 인해 투자에 쉽게 나설 상황이 아니 라는 것이다.
도이치뱅크의 경우 인더스트리 4.0이 마케팅 용어 로 사용되면서 그 의미가 점점 과장되어 간다고 지적하며, 몇 년 안에 잊혀진 단어가 될 수 있다고 경고하기도 했다.
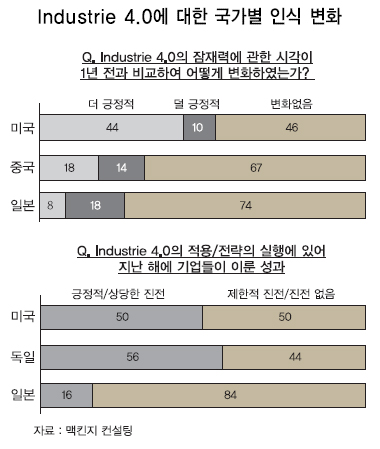
스마트 팩토리로 제조업 부흥 프로젝트 가시화
이러한 부정적인 전망은 제조업 부흥 프로젝트를 추진 중인 각 국의 정부가 더욱 잘 이해하고 있다.
그만큼 이상적인 비전보다 는 이 프로그램들을 통한 가시적인 성과가 필요한데, 추진 주체들은 스마트 팩토리에서 그 답을 찾고 있다.
실제로 대부분의 프로그램이 스마트 팩토리 구축을 최우선 과제로 선정하고 있다.
스마트 팩토리는 다른 기기나 서비스의 스마트화와 마찬가지로 공장이 스스로 판단하고 이에 따라 작업을 수행할 수 있는 지능화된 공장을 의미한다.
즉, 우리 주 변에서 진행되고 있는 사물인터넷화가 산업현장에서 진행되는 것이다.
상대적으로 신기술에 열려 있는 B2B(Business-to-Business) 시장인 만큼 비용 혹은 수익측면 에서 가시적인 효과를 가져올 경우, 스마트 팩토리는 B2C 시장에 비해 빠르게 확산 될 가능성이 있다.
이러한 스마트 팩토리는 기존에 오랫동안 논의되어 온 공장자동화와 유사하다고 여겨질 수 있다.
하지만, 단순히 사람의 노동력을 대체하는 공장자동화에서 한 발 더 나아가, 스마트 팩토리는 다양한 장소에서 다양한 방법으로 수집된 정보를 바탕으로 공장 스스로 공정 최적화나 생산 스케줄 수립 등과 관련된 의사결정을 내릴 수 있다는 점에서 큰 차이를 보인다.
제조 현장에서의 정보뿐만 아니라 가치 사슬 상에서 실 시간으로 발생하고 입력되는 모든 정보에 따라 최적의 의사결정을 내리는 것이다.
다만 아직까지 현실적으로 스스로 정보를 판단하는 인공지능 수준의 시스템 구축은 쉽지 않은 상황이며 대부분 기계의 가동 상태, 기계의 파손 및 제품의 하자 발생 가능성 판단 및 예측, 원격 관리 등을 통한 장비의 효율 및 안정성 확대, 생산성 향상, 비용 절감에 초점을 두고 있다.
한편 스마트 팩토리가 성공하기 위해서는 독립적인 공장 하나의 시스템만이 중요한 것이 아니라, 그 공장에 부품과 재료를 제공하는 공급업체들까지도 서로 연결되어 최적화 되어야 한다.
하지만 많은 공급업체들이 중소기업인 점을 감안한다면 현실적으로 이들 모두를 스마트 팩토리로 만드는 것이 쉽지 않기 때문에 정부가 적 극적으로 나서고 있다.
독일의 경우 중소기업의 참여를 더욱 독려할 수 있는‘플랫폼 인더스트리 4.0’을 추진하기 시작했다.
‘제조업 3.0’을 내걸고 있는 우리나라에서도 정부는 대기업보다 중소기업에 초점을 맞추어 프로그램을 진행하고 있으며, 2020 년까지 1만개의 스마트 공장 구축을 목표로 내걸고 있다.
그러나 단일 공장 내 스마 트화 뿐 아니라 공장들 간에 서로 연결된 시스템을 갖기까지는 적지않은 시간이 소요될 것으로 예상된다.
전 세계가 관심을 갖는 대표 스마트 팩토리
스마트 팩토리의 대표적인 사례로는 지멘스의 암베르그 공장을 꼽을 수 있다. 자동 화수준은 75%에 이르며, 1,000여 종류의 제품을 연간 1,200만개 생산하고 있다.
설계 및 주문 변경에도 99.7%의 제품을 24시간 내에 출시하는 시스템을 구축하고 있으며, 100만 개당 불량수는 약 11.5개에 불과할 정도로 높은 품질을 유지하고 있다.
GE 역시 스마트 팩토리 구축에 적극적으로 나서고 있다. ‘생각하는 공장 (Brilliant Factory)’라고 명명된 GE의 스마트 팩토리는 인도 푸네에 처음 설립되었다.
데이터를 기반으로 설비의 돌발적인 정지를 예방할 뿐 아니라 제품의 생산량 및 품종 등이 자동 조절되고 있다.
이로 인해 생산성이 약 10% 가량 향상되었다는 것이 GE측의 설명이다. 이러한 경험을 바탕으로 GE는 전 세계에 흩어져있는 400여개의 공장 가운데 50여개 공장으로 생각하는 공장을 확장할 계획이다.
3. 스마트 팩토리의 지향점
BCG가 미국 제조업체 경영자를 대상으로 한 설문조사에 따르면 향후 5년 안에 스마트 팩토리 구축과 관련된 투자를 진행할 예정이라고 답한 사람이 70%가 넘었으며, 응답자의 약 3/4은 이러한 투자를 통해 생산성을 향상시킬 수 있을 것이라고 기대하는 것으로 나타났다.
독일의 경우 인더스트리 4.0을 통해 약 30%까지 생산성을 향상시킬 수 있다고 예상한다.
GE는 스마트 팩토리를 통해 제품 개발 사이클을 20% 단축하고, 제조공정과 공급망에서의 생산성을 20% 향상시킬 것으로 기대하고 있다.
하지만 생산성 향상으로 스마트 팩토리 도입 목표를 달성했다고 보기는 어렵다.
중국과 인도 등 신흥 제조 강국들이 스마트 팩토리 구축에 경쟁적으로 나서고 있는 만큼, 생산성 향상만으로는 신흥국 제조업체와의 경쟁에서 우위를 점하기는 쉽지 않을 것으로 보인다.
결국 스마트 팩토리의 지향점은 생산성 향상보다는 제품 경쟁력의 향상과 이에 따른 기업의 경쟁력 강화여야 하는 것이다.
즉 공장만의 혁신이 아니라, 기업 차원 에서 혁신이 이루어져야 스마트 팩토리가 진정한 의미를 갖는다.
맞춤형 대량생산
제품이 경쟁력을 갖기 위해서는 결국, 소비자가 원하는 제품을 제때 생산에 반영하여 발빠르게 출시할 수 있는 능력을 갖추어야 한다.
소품종 대량생산을 통한 생산성 강화가 아니라 고객 개개인의 니즈를 반영하여 제품을 맞춤화할 수 있는 맞춤형 대량생산(Mass Customization) 전략이 필요하다.
독일과 미국 등에서는 스마트 팩토 리를 통해 이를 달성하는 것을 목표로 하고 있다.
물론 이미 선진 제조업체들은 유연 생산 시스템을 도입하여 한 생산라인에서 다 품종 생산이 가능한 체계를 구축해 놓고 있다.
스마트 팩토리는 이러한 유연 생산 시스템을 한 단계 더 향상시키는 것을 목표로 한다.
즉 품종의 증대 수준이 아니라, 고객 개개인의 주문 사항에 따라 즉각적으로 공정 라인이 바뀌며 제품을 생산할 수 있는 수준까지 달성하겠다는 것이다.
물론 대량 생산 방식과 비교했을 때 비용, 품 질, 납기일의 수준을 유지하는 것은 당연하다.
이를 구현하기 위해서는 몇 가지 기술들이 필요한데, 대표적인 것이 CPS(Cyber Physical Systems)라고 불리는 가상물리 시스템이다.
이는 물리적 세계와 사이버 세계를 연결하 는 통합 시스템을 의미하는데, 쉽게 말해 현실 세계를 그대로 사이버 세계에 구현한다는 개념이다.
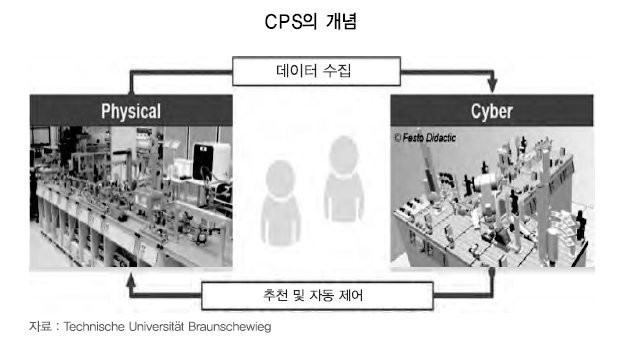
이럴 경우 맞춤형 생산을 위해 공장의 라인 을 교체할 때 물리적으로 바로 수정하면서 시행착오를 겪기보다는 사이버 세계에서 먼저 변화를 시뮬레이션한 후 이를 현실 세계에 반영할 수 있다.
그만큼 생산라인의 유연성을 더욱 높일 수 있다.
여기에 CPS의 지능화가 한층 고도화될수록, 자율적 의사 결정이 가능해지기 때문에 고객 니즈 변화에 따라 공정 역시 즉각적으로 변화시키기가 훨씬 수월해 질 수 있다.
한편 CPS는 시스템뿐 아니라 생산된 제품까지도 확장 적용될 수 있다.
즉 물리 적 세계의 제품과 동일한 사이버 제품을 스마트 팩토리에 저장한다는 개념인데, 이 때 사이버상에 저장된 제품을 디지털 트윈 혹은 사이버 클론 등으로 칭한다.
이러한 시스템이 구축된다면, 맞춤형으로 생산된 수많은 제품 하나하나를 저장하여 각 각의 상태를 추적하는 것도 가능하게 되는 것이다.
또 다른 필요 기술로는 생산라인의 모듈화를 들 수 있다. 즉 생산 라인을 모듈로 구성해, 제품 생산에 필요한 모듈을 그때 그때 조립식으로 붙이고, 필요없는 모듈은 즉각 이동시켜 라인에서 제외할 수 있는 방식을 구현하는 것이다.
고정된 라인에서는 급격한 생산 비용 증가로 인해 다변화된 고객의 니즈를 충족시킬 수 없었으나, 모듈화를 통해 유연성을 확보한 생산라인은 고객의 니즈에 따라 맞춤형 생산이 가능해져 제조기업으로 하여금 고객에게 차별적 가치를 제공할 수 있게 한다.
2014년 하노버 산업박람회(Hannover Messe)에서 독일의 독립연구기관인 스마트팩토리 KL(SmartFactoryKL)은 이러한 모듈화된 시스템을 선보여 주목을 받기도 했다.
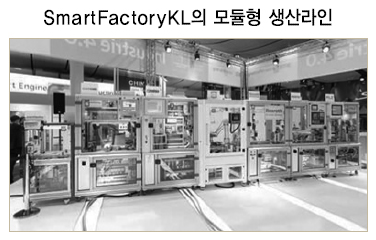
당시 선보였던 시연회에 따르면 수분 내로 모듈 순서의 변환이 가능해, 맞춤형 생산에 대한 기대감을 한층 높였다.
CPS나 생산라인 모듈화의 경우 아직 실제 공장에서 제대로 구현되지는 못하고 있는 기술들인 반면, 당장 적용 가능한 기술들도 있다.
맞춤형 생산에서 작업자들이 그 모든 품종에 적합한 최적의 작업방식을 완전히 습득하고 있기는 어렵다.
따라서 적절한 작업 지시나 지원은 필수적이다.
실제로 스마트 팩토리를 표방하는 많은 공장에서는 곳곳에 작업 지시 및 지원을 위한 디스플레이가 설치되어 있는 경우가 많다.
심지어 BMW는 웨어러블 기기를 이용해서 개별 작업자 수준에서 작업 지시와 지원을 하고 있다.
뮌헨과 라이프치히 공장에서는 스마트워치를 통한 작업지시를 시범 운영 중에 있으며, 미국 스파턴버그 공장에서는 구글글래스를 통한 제품 검수 및 음성/동영상 보고를 테스트 중에 있다.
또한 반복적이지만, 부분적으로 차이가 있는 업무들에 대해서는 작업자가 로봇과 협업할 수 있는 시스템도 상용화되었는데, BMW의 경우 뮌헨과 스파턴버그 등의 공장에서 이를 적용하기도 했다.
이러한 기술들을 기반으로 BMW는 맞춤형 대량 생산에 도전하고 있는데, 소비자가 차량 색상, 인테리어, 인포테인먼트 시스템 등을 직접 선택하면, 이를 기준으로 개별 고객 맞춤형 제품을 생산하는 시스템을 구축하였다.
이는 이미 생산 된 차량 가운데 소비자가 선택한 옵션과 동일한 자동차를 찾아 배달하는 시스템이 아니라, 아예 소비자의 선택 사항을 공장에 전달하여 각각의 고객이 원하는 제품을 생산하는 것이다.
서비스화의 추진
제품 경쟁력 강화를 위한 또 다른 방법은 서비스와 연계하여 제품의 활용성을 높이는 것이다.
이러한 제조업의 서비스화는 이미 장비 업체들을 중심으로 널리 퍼져있는 B2B 비즈니스 형태이다.
즉 판매된 장비에 센서를 통해 고장상태를 파악하거나 향후 고장을 예측하여, 장비가 멈추는 사고를 사전에 예방해주는 것이다.
이뿐 아니 라 제품의 새로운 이용가치를 제안하고 부가제품 판매의 기회로 활용되기도 한다.
얼핏 보면 제조업의 서비스화는 비즈니스의 이슈일 뿐 공장과는 무관할 수도 있다.
하지만 스마트 팩토리 관련 기술을 통해 서비스화가 한층 강화될 수도 있다.
CPS를 갖추고 있게 되면, 판매된 장비나 제품들에 대한 데이터가 공장에 축적되므로 각 제품의 상태를 추적하여 그에 적절한 서비스를 사전에 고객에게 제안할 수 있기 때문이다.
다시 말해 다양한 데이터를 수집하여 장비나 제품의 정확한 마모 상태를 예측하거나, 나아가 장비나 제품의 성능에 영향을 줄 수 있는 상황까지 고려하여 고객이 필요성을 인지하기 전에 미리 서비스를 제공하는 것이다.
장비업체인 지멘스의 경우 전세계 28만 개의 장비에 센서를 탑재하여 데이터를 수집하며 가동률과 불량률을 실시간으로 체크하고 있다.
매일 5,000만건 이상의 제조 현장의 데이터를 수집하고 이를 바탕으로 1/1,000초 단위로 작업을 분석하여 개선 방안을 모색한다.
가동률, 불량률 등을 실시간으로 체크하고 최적 공정을 초단위로 예측한다.
이러한 생산 시스템을 갖춘 지멘스는 자사의 생산성 개선에 머무르지 않고 이러한 생산 시스템을 외부에 판매하여 수익을 올리고 있다.
암베르그공장의 성공 사례를 바탕으로 BMW, 마세라티 등으로 외판을 확대하며 새로운 사업기회를 열어가고 있다.
이를 기반으로 ‘부품’을 판매하는 기업에서 산업자동화‘시스템’을 제공하는 서비스 기업으로 사업 모델을 전환하고 있다.
GE 역시 서비스화를 추진하고 있다.
GE의 Brilliant Factory 비전을 다양한 업 종, 다양한 이용환경, 다양한 업체들로 확장하기 위한 플랫폼인 Predix를 출시하였다.
Predix는 클라우드 기반의 데이터 분석 서비스이다.
항공기 엔진이나 발전소 터빈 등에 수많은 센서를 부착하여 수집된 데이터를 활용하여 제품의 성능 향상에 적극적으로 나서고 있다.
항공기 엔진 등 항공 분야에서 축적된 데이터와 명성을 바탕으로 항공기 연료 절감, 고장 예방 등 솔루션 사업으로 사업 영역을 확장해 가고 있다.
이러한 성능 향상은 GE의 제품과 서비스를 이용하는 클라이언트들에게 즉각적인 보상이 된다.
항공 엔진의 경우 알이탈리아 항공에 제공하였는데, 도입 첫해 연료비의 1.5%, 금액으로 환산시 약 1,500만 달러를 절약할 수 있었다.
한편, 이러한 서비스화의 추세는 단순히 제조업체가 서비스를 제공한다는 것 이상을 의미할 수 있다.
즉 서비스를 통한 추가적 수익 확보를 넘어서, 아예 서비스가 중심이 되는 비즈니스로 진화도 가능하다는 것이다.
World E c onomic Forum(WEF)은 이를 네 가지 단계로 설명하고 있다.
먼저 자산의 운영 효율성을 높여주는 단계가 첫번째인데, 여기에는 제품의 활용성을 높이거나, 가동비용을 절감하는 등의 서비스를 제공하는 것을 말한다.
두 번째 단계는 서비스를 제품과 함께 판매하는 단계이다.
소프트웨어를 기반으로 하는 서비스를 판매하거나, 데이터를 수익화하는 단계를 말한다.
앞서 언급했던 지멘스나 GE 등이 이러한 단계에 이미 올라선 사업자들이다.
세 번째 단계는 제품이나 서비스를 판매하는 수준을 넘어서 측정가능한 구체적인 성과(Measurable Outcome)가 판매되는 단계이다.
쉽게 말해 장비업체의 클라이언트가 원하는 성과를 판매하는 것을 예로 들 수 있다.
냉방 기기의 예를 든다면, 냉방기기를 파는 단계, 냉방서비스를 파는 단계를 넘어‘쾌적한 냉방상태를 유지하며 에너지를 절감하는 성과’를 판매하는 단계이다.
이럴 경우 클라이언트가 거둔 성과를 기반으로 수익을 배분받는 방식의 비즈니스 모델도 가능하다.
네 번째 단계는 세 번째 단계에서 한층진화하여 연속적으로 수요를 감지하여, 성과를 판매할 수 있는 서비스를 지속 제공하는 단계이다.
중요한 점은 이러한 서비스화는 단일 기업이 달성할 수 있는 범위를 넘어서는 경 우가 많다는 것이다. 따라서 이들 기업들이 서로 유기적으로 연결되는 생태계가 형성될 것으로 예상된다.
4. 맺음말
인터넷이 보편화된 지 20여년 밖에 지나지 않았지만, 소비자들의 삶을 크게 바꾸었으며, 구글, 페이스북, 아마존과 같은 거대기업들도 탄생했다.
이제 인터넷이 IoT 기술을 기반으로 산업인터넷이란 형태로 산업계에 확장되어 가고 있다.
이러한 산업인터넷은 반도체기술, 통신기술, 센서기술, 인공지능의 기술과 맞물리며, 또 한 차례 산업의 큰 격변을 몰고 올 것으로 전망된다.
물론 4차 산업혁명에 대해 실체가 없다는 비난도 있다.
특히 인더스트리 4.0과 같은 프로그램이 등장하면서 마케팅 수단, 기술적 우위를 과시하기 위한 수단이라 는 세간의 평도 있다.
그러면서도 또 한편으로는 많은 업체들이 이러한 변화를 생각하고 있고 뒤처질세라 두려워하고 있지만 제대로 대응하지 못해 불안해 하기도 하 는게 현실이다.
한때의 유행은 아닐지, 어떻게 시작해야 하는지, 투자 성과는 가능한지, 시스템의 안정성과 신뢰성을 담보할 수 있을지 등에 대한 의심과 불안이 클 수 있다.
그러나 기기의 오작동이 사람의 안전과 직결될 수 있는 자동차 산업에서도 자동차 전장시스템과 전기자동차의 확대, 무인자동차시대의 도래를 되돌릴 수 없듯 이 산업인터넷을 중심으로 한 산업현장의 변화의 대세도 되돌려지지 않을 것이다.
도이치 뱅크의 지적대로 인더스트리 4.0이나 스마트 팩토리와 같은 용어는 얼마 가지 않아 사라질 수는 있지만, 산업인터넷으로 인한 혁신이 없어지지는 않을 것이다.
당장은 스마트 팩토리에서 시작되고 있지만 점차 단일 공장에서 여러 공장간의 연결, 공급망과의 연계 등으로 확장되며, 점차 서비스화가 진화될 것이다.
충족하려 는 수요 역시 좋은 제품, 값싼 제품에서 맞춤형 제품으로, 궁극적으로는 수요의 목적, 제품구매의 이유(Why behind Buy)를 찾아 근본적으로 해결하려는 방향으로 갈 것으로 전망되고 있다.
예를 들어 안전하고 빠르고 쾌적한 항공서비스를 저렴한 합리적인 가격에 제공하기 위해서는 항공 엔진의 성능, 항공기 정비, 항공기 노선 조정 등이 모두 유기적으로 연결되어야 경쟁력 있는 서비스가 가능해진다.
즉 단일 기업이 모든 문제를 해결할 수 없고 관련 생태계의 기업들과 유기적으로 연계되어야 한다.
미국의 IIC가 추구하는 것의 상당부분도 궁극적으로 연결 협력할 수있는 생태계의 조성에 맞춰져 있다.
스마트 팩토리에서 시작하여 가능한 발전 단계를 따라가다 보면 제품이 아닌 서 비스, “Why behind Buy”로 발전하고 이는 산업생태계로 이어질 수 있다.
GE 등의 기업들이 Predix와 같이 기업내 플랫폼만이 아니라 다른 기업들의 참여가 가능한 플랫폼을 지향하고 있는 것도 이런 변화를 생각하고 관련 생태계에서의 주도적인 역할을 추구하는 것으로 보인다.
산업인터넷 혁명은 아직 개념적으로 보일 수 있다.
사례도 아직 일부 분야에 머 무르고 있고 보편적인 트렌드가 될 수 있을지 회의적인 시각들도 있을 수 있다.
그리고 범용성이 약하고 신뢰성이 중요한 산업분야에서 소비시장에서와 같이 변화가 급격하게 진행될까라는 의문도 가능하다.
그러나 시간이 좀 걸릴 수는 있을지 몰라도 그 방향은 틀리지 않을 것으로 보인 다는 것이다.
스마트 팩토리는 그 변화가 수면 위로 드러난 모양, 변화의 서곡일 가능성이 있다.
그리고 구글, 페이스북이 등장했듯이, 산업인터넷을 장악하는 제2의 구글과 페이스북이 등장하게 될지도 모른다.